We have the top qualified Injection moulding widely used process for producing plastic parts with complex geometries. At our facility, we use the advanced injection moulding machines to manufacture many different non-metallic components for vehicles. At IGS we have all sorts of top quality high standard machines to meet your standards.
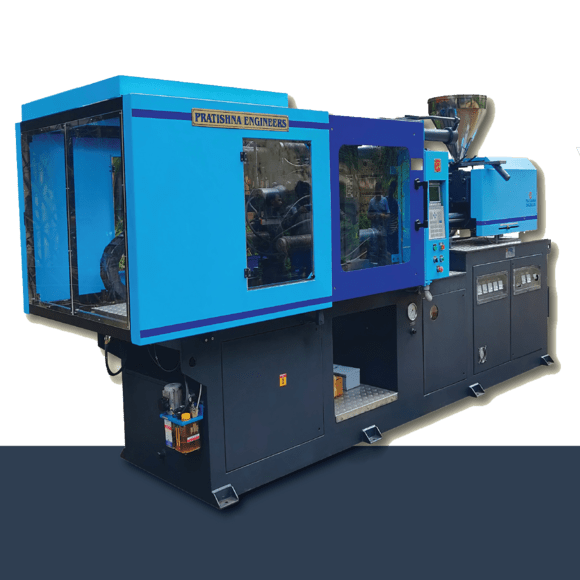
How Injection Molding Machines Work?
An injection moulding machine consists of a material hopper, an injection unit, a heating unit, and a mould clamping unit. What do our injection moulding machines do is listed below,
- Plastic pellets or granules are fed from the hopper into the heated barrel of the injection unit.
- A reciprocating screw rotates and moves forward, shearing and melting the plastic material.
- The molten plastic is injected under high pressure into the mould cavity.
- The mould, made of two or more sections, is clamped shut to prevent the molten material from escaping.
- After cooling and solidification, the mould opens, and the ejector system pushes out the finished part.
Our professionals are aware that Accurate control over temperature, pressure, and timing is extremely essential for producing high-quality moulded parts with consistent dimensions and properties because we love what we do.
Applications in Automotive Manufacturing
Interior trim components (dashboards, door panels, consoles)
Exterior body components (bumpers, grilles, spoilers)
Under-the-hood components (air intake manifolds, throttle bodies)
Lighting components (headlight housings, reflectors)
Electrical components (connectors, switch housings)
By carefully selecting the appropriate plastic materials (such as ABS, polypropylene, or engineering-grade resins) and optimising the moulding parameters. We ensure that these injection-moulded parts meet stringent performance, best safety, and aesthetic requirements for automotive applications because we understand the needs of our clients.